Choosing the right coupling for your business is essential for keeping your equipment running smoothly and efficiently. Whether you’re in manufacturing, construction, or any other industry that relies on machinery, selecting the perfect coupling can improve performance, reduce downtime, and save money in the long run. In this guide, I’ll walk you through everything you need to know about couplings, from the different types available to factors like material selection and maintenance. By the end, you’ll have the knowledge you need to make the best decision for your business.
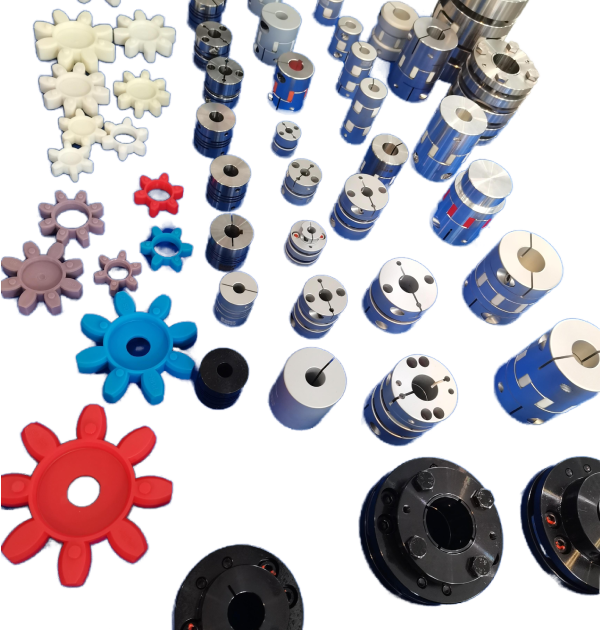
What is a Coupling and Why is It Essential for Your Business?
At its core, a coupling is a mechanical component used to connect two shafts together to transmit power. It ensures that the two parts rotate together in sync, which is critical for machinery to function properly. Without the right coupling, equipment may experience misalignment, excessive vibration, or even failure. So, understanding couplings and their importance is key to maintaining the smooth operation of your business.
Types of Couplings: Which One Is Right for Your Equipment?
Not all couplings are the same, and the type you choose should be tailored to your specific needs. Here are some common coupling types:
- Rigid Couplings – These couplings don’t allow for any misalignment between shafts and are ideal for applications where precise alignment is critical.
- Flexible Couplings – These allow for some movement and are perfect for compensating for misalignment or shaft vibration.
- Fluid Couplings – These use a liquid to transmit torque and are great for applications where smooth starts and controlled acceleration are needed.
- Universal Couplings – These are designed to handle angular misalignment and are commonly used in automotive and industrial equipment.
Each coupling type serves a different purpose, and it’s important to choose the one that aligns with your business’s machinery and its requirements.
Key Factors to Consider When Selecting a Coupling
When selecting the right coupling, it’s crucial to keep the following factors in mind:
- Load Capacity – Ensure that the coupling can handle the torque or load your machinery will experience. Overloading can lead to premature failure.
- Misalignment Tolerance – Determine how much misalignment your equipment can tolerate and choose a coupling that accommodates it.
- Speed and Performance – Some couplings are designed for high-speed applications, while others work better for low-speed, high-torque environments.
- Environmental Conditions – Consider factors such as temperature, humidity, and exposure to chemicals when selecting materials for your coupling.
By evaluating these factors, you can make a more informed choice and avoid unnecessary maintenance or repairs.
How to Match a Coupling to Your Business’s Specific Application
Every business has unique requirements when it comes to coupling selection. Some industries require high precision, while others need flexibility to handle variable conditions. Take time to analyze the specific needs of your machinery and its operating environment. For example, if you’re in a high-vibration industry, you may need a coupling designed to absorb shock. On the other hand, if precision is key, a rigid coupling might be your best bet.
Common Mistakes Businesses Make When Choosing Couplings
Many businesses make the mistake of choosing a coupling based solely on cost or convenience. While these factors are important, they shouldn’t be the only ones to consider. Here are some common mistakes:
- Ignoring Misalignment – Not accounting for shaft misalignment can cause vibrations, increased wear, and eventually, equipment failure.
- Choosing the Wrong Material – Using a material that’s too weak for the application or not resistant to environmental factors can lead to premature wear and tear.
- Overlooking Maintenance – Failing to maintain couplings can result in significant damage to the equipment, leading to costly repairs.
Avoiding these mistakes will help you extend the lifespan of your couplings and prevent downtime.
The Role of Material Selection in Coupling Durability
Material selection is crucial in determining the lifespan and performance of your coupling. Common materials include steel, aluminum, bronze, and various plastics. Each material has its own set of properties:
- Steel – Known for its strength and durability, steel is often used in high-torque applications.
- Aluminum – Lightweight and resistant to corrosion, aluminum is great for applications that need to minimize weight.
- Bronze – Offers high resistance to wear and is ideal for applications with high shock loads.
- Plastic – Lightweight and cost-effective, plastic couplings are suitable for low-load, low-speed applications.
By understanding the pros and cons of each material, you can make an informed decision based on your business’s needs.
How to Properly Install a Coupling: Tips for Businesses
Correct installation is key to ensuring that your coupling functions properly and lasts as long as possible. Here are some important tips:
- Align the Shafts Properly – Misalignment can cause premature wear or failure, so be sure to align the shafts accurately during installation.
- Check for Proper Fit – Make sure the coupling is the correct size and fits snugly on the shafts.
- Tighten Bolts Evenly – Ensure that bolts are tightened evenly to avoid uneven stress on the coupling.
- Test the Installation – Run the equipment at low speed initially to check for vibrations, noise, or misalignment.
Proper installation can prevent costly mistakes and extend the life of your coupling and equipment.
Maintenance and Care: Ensuring Longevity of Your Coupling
Maintaining your coupling is essential to keeping your business running smoothly. Here are a few maintenance tips to consider:
- Regular Inspections – Periodically inspect the coupling for signs of wear, corrosion, or cracks.
- Lubrication – Ensure that the coupling is properly lubricated to prevent friction and wear.
- Replace Damaged Parts – Don’t wait for a complete failure. Replace worn or damaged parts before they cause bigger issues.
Proper maintenance reduces the likelihood of unexpected downtime and keeps your equipment in top shape.
How to Identify When a Coupling Needs to Be Replaced
Couplings don’t last forever, and knowing when to replace them can save you from costly downtime. Signs that it may be time to replace your coupling include:
- Excessive Vibration – If the coupling is no longer absorbing shock properly, it could indicate wear.
- Noise – Unusual noises, such as squealing or grinding, are often signs of misalignment or damage.
- Visible Damage – Cracks, dents, or significant wear on the coupling are clear indicators that it needs to be replaced.
By being proactive about replacing worn couplings, you can avoid unexpected failures and ensure smooth operations.
Choosing Between Standard and Custom Couplings for Your Business
While standard couplings may work for many businesses, custom couplings can offer a better fit for unique needs. Custom couplings can be designed to handle specific load requirements, environmental conditions, or operational demands. However, they come at a higher cost and longer lead time. It’s important to weigh the benefits against the added expense and decide if a custom solution is the right choice for your business.
Conclusion
Choosing the right coupling is more than just picking the most affordable option—it’s about selecting the right solution that ensures your equipment runs smoothly, safely, and efficiently. By considering factors like load capacity, misalignment tolerance, material selection, and maintenance, you can make a choice that best fits your business’s needs. With the right coupling in place, your operations will run with less downtime and better performance, saving you time and money in the long run.